Moving Energy Forward
Case Studies
Preparation of a Turn Around (TA)
A Turn Around (TA) is a crucial part of the life of a refinery, as the whole plant is shut down and major improvements are installed, setting up the asset for more efficient activities for the next six years.
From an HSEC point of view, it presents many opportunities, as the new equipment and improved units will reduce people’s exposure to incidents and reduce the impact on the environment. But as the shutdown will see the refinery’s workforce increase tenfold, thorough preparation is required.
The preparation of the 2023 TA for Ingolstadt started in 2021. Since the beginning a Health, Safety and Environment (HSE) coordinator was nominated and worked closely with the TA and project teams to tackle HSE aspects right from the beginning. All activities to be carried out were mapped, hazardous activities were identified (heavy lifting, confined space entry, etc.), and a dedicated risk assessment was performed. These efforts ensured the right skills and resources were assigned and sufficient control and safety measures were defined. Major contractors, whose scope comprised critical or high-risk activities were asked to develop their own safety plans to be presented to the refinery management.
Our mapping and the contractors’ plans formed the basis of our “fire watch” concept, allowing for recruitment of dedicated and trained resources. Beyond monitoring the work itself, they would also observe interfaces between the different work groups in the field and help identify and solve issues as required.
Daily meetings with the safety leaders from all companies involved were to be held to share experiences from the day and night before, including observations which required corrections, so that instructions and learning could be transferred to the teams on their daily safety talks.
All efforts have been put in place to minimise the incidents during the shutdown and the safety and environmental performance will be closely monitored.
While the results of the TA will be covered in a subsequent edition of this report, the projects within its scope are worth noting:
- More efficient use of heat energy: Maximise the use of produced heat within the system, by installing new, more efficient air coolers and adding tie-ins so that the heat produced at the top of the distillation column becomes the energy source for a boiler of light product in the catalytic cracking unit. This project has a direct impact on the greenhouse gas emissions of the refinery.
- More power for the district heating system: Improve the process to provide waste heat to the district heating system. This reduces the area’s greenhouse gas emissions by avoiding the production of additional heat by the local community. As much as 10% of the refinery’s direct emissions are saved.
- Less Air Emissions: Preparing the plant for the finalisation of our MINERVA project (see previous edition of this report) and reduce the sulphuric dioxide (SO2) emissions of the refinery.
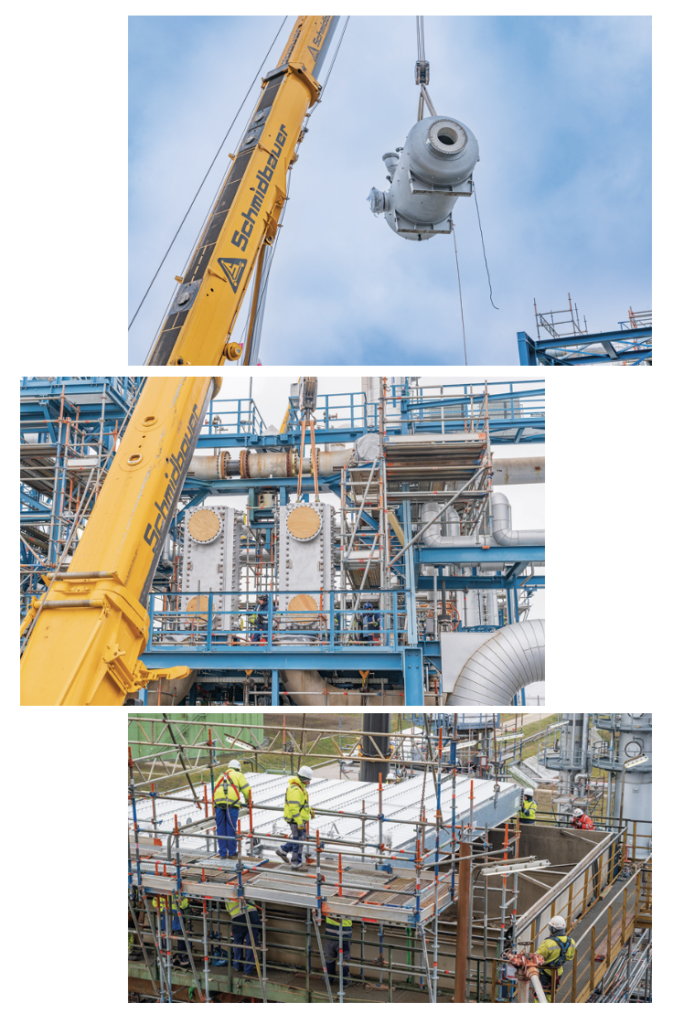